Our Work Experience
- Software Engineering, Development, Programming, and Network Support
- Information System (IS) Development, Information Assurance (IA), and Information Technology (IT) Support
- Program & User Management
- Enterprise Support Services: Technical, Administrative, and Business Process Support
- Logistics
- Financial and Audit Readiness
- Database Administration & Support
- Data Architecture & Modeling
- Analysis and Testing
- Training and Knowledge Management
Software Engineering, Development, Programming, and Network Support
Application support, help desk end-user support, issue resolution, data integrity, deficiency identification, SAP deployment and execution, utility software tool maintenance
Herdt supports NAVSUP’s Navy ERP (SAP) solution and NAVSUP’s EBO along their numerous DON customers with Navy ERP software, data, and business process sustainment activities. We provide business process support, benefits realization, requirements analysis, testing, help desk end-user support, issue resolution, deficiency identification, user and role resolution management, data integrity, data management, organizational change management, training curriculum and master training schedule management, and customer advocacy to almost 10,000 end users.
Herdt supported the NAVSUP EBO in developing the AIT requirements for NAVSUP, Navy Supply and Hazardous Material (HAZMAT). Herdt’s support to NAVSUP EBO encompasses the entire life cycle management process, including planning, designing, testing, training, and deploying SAP into production.
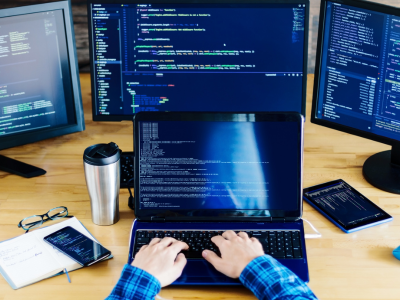
Herdt provides NAVSUP and USMC LOGCOM SMAG with support services in SAP deployment planning and execution; utility software tool maintenance; cutover planning and execution; catch-up planning and execution; data management; project management, scheduling and go live support; legacy integration with Navy ERP at NAVSUP and other Navy/USMC SYSCOMs; enterprise integration; Navy Warehouse Enterprise System support of Navy ERP for sustainment as well as future site implementations and integrated Automated Identification Technologies (AIT) solutions; and end-user training and Knowledge Transfer.
Herdt implemented new interfaces to Navy ERP for the Marine Corps Procurement Requisition System for procurement, Standard Procurement System (SPS) repair supply scenarios, and Master Data Repository for reporting and supply planning data.
With each software release, we conduct continuous process improvement reviews and document lessons learned. Herdt reviews/maintains/configures/manages Navy ERP authoritative documents such as Requirements Statements, Functional Design Specifications (FDSs), Technical Design Specification, Technical Functional Specifications, Emergency Work Request, Requirements Traceability Matrices, Test Plans, User Guides, Training Guides, Desk Guides, Lessons Learned, Implementation Plans, Incident Reports, Plan of Action and Milestones (POA&Ms), Interface Control Agreements (ICAs), Memorandums of Agreement (MOAs), white papers, and detailed progress reports.
Herdt managed the process of creating and reviewing Test Scripts. We support testing phases within Navy ERP using HP Quality Center (HPQC) Application Life Cycle Management (ALM) software to standardize testing. Implementation best practice examples include 15 Business Transition Plans (BTP) that we analyzed, consolidated, and completed based on a combination of trouble tickets.
We assisted in developing the requirements traceability matrix and reconciling consolidated cross-SYSCOM business requirements across six process areas: Printing, Goods Receipt/Issue/Transfer, Put-away, Physical Inventory, User Interface, and Hardware requirements. This included the 261 detailed NAVSUP and HAZMAT requirements for resolution. We also assisted in developing the NAVSUP AIT Concept of Design and provided continuous feedback to the government team for funding strategies.
Information System (IS) Development, Information Assurance (IA), and Information Technology (IT) Support
Network Support; Configuration Management (CM) Support; Quality Assurance (QA) Support; Information System (IS) Development, Information Assurance (IA), and Information Technology (IT) Support
Herdt has 20 years of experience supporting Navy ERP across multiple Navy and Marine Corps commands, including SSP, BUMED, PMW 220, NAVSUP, NAVSEA, NAVAIR, NAVWAR, ONR, CNRF, CNIC/NAVFAC, FLEETS/RESFOR, and USMC LOGCOM. Herdt supported the go-live of Navy Research Laboratory, Naval Facilities Engineering and Expeditionary Warfare Center, NAVAIR Commander, Fleet Readiness Centers, and USMC LOGCOM’s Supply Management Activity Group (SMAG) and Depot Management Activity Group (DMAG).
Herdt performed requirements analysis, architectural design and modeling, installation and integration support, database administration, migration of NAVSEA legacy shipyard financial system data over to S/4HANA, system and acceptance testing, training and operational documentation, system software design documentation and implementation of maintenance and system enhancements for the S/4HANA-based Navy Maritime Maintenance Enterprise System – Financial System (NFS) solution.
Our ERP Central Component (ECC) functional support includes Asset Management (AM), Inventory Management/Warehouse Management (IM/WM), Order Fulfillment (OF), Business Objects (BObj), Material Management-Procurement, Sales & Distribution (SD), Finance (FI), Funds Management (FM), Controlling (CO), Project Systems (PS), User Management, and Planning/SAP SCM.
Herdt performs evaluations of new technology tools/methodologies and continuously researches and recommends technology to NAVSUP as it becomes available. Examples are SAP Knoa to optimize the performance of Navy ERP and user experience management, and SAP Enable Now to improve productivity, user adoption, and the end-user experience. These capabilities allowed Herdt to create, maintain, and deliver performance support, learning material, and documentation content. This new technology provided the foundation of our Online Training (OLT), saving millions of dollars over the last three years of training delivery.
Herdt managed the process of creating and reviewing Test Scripts. We supported testing phases within Navy ERP using HP Quality Center (HPQC) Application Life Cycle Management (ALM) software to standardize testing. Our proven easy-to-use templates allowed end users to create test scripts in Microsoft Excel that can be imported into HPQC ALM, reducing the time and cost of test scripting. We created and provided detailed instructions for executing the test scripts, standardizing and customizing script attributes for regression testing scope analysis, and creating user friendly HPQC reports to manage the testing through completion.
Herdt is familiar with UiPath RPAs used at NAVSUP, NAVWAR, and BUMED. We have our own UiPath-trained personnel and an established relationship with a small business we can engage as needed. They are a UiPath Gold Partner and have completed the UiPath Services Network (USN) program – putting them in the top 5% of UiPath’s partners.
Program & User Management
Program management & support, customer liaison business office support, user management (UM), access violation management (AVM)
Herdt supports various NAVSUP meetings, Drumbeats, Release Planning, Working Groups, and Boards, where we collaborate with key stakeholders, other customer organizations, and related process owners. We also maintain documentation and updates from these meetings, including system requirements, discussion items, white papers, and design changes, as well as create meeting agendas and minutes. We actively participate with expert analysis, status reports, reviews, and recommendations.
Herdt’s User Management (UM) Command Liaisons at NAVSUP EBO process requests to create, reactivate, or terminate accounts and to submit changes to user role assignments or updates to Navy ERP personal data by using the Naval Identity Services’ (NIS) Identity, Credential and Access Management (ICAM) program.
We support NAVSUP EBO as the lead for SOD reviews, user access, and current authorizations.
We support PMW 220 Access Violation Management (AVM) reviews, cross-SYSCOM UM calls, UM Working Group (UMWG) meetings for role changes, and additional meetings.
Herdt closes out an average of over 70 User Management-specific NHDSM tickets monthly, 85% of which required no further action. We provided training and assistance, from implementation to sustainment, for SMAG’s new UM lead, including SOPS, Guides, and Instruction documents in processing Access Enforcer Requests and NIS ICAM.
Herdt has provided program management support to the NAVSUP, NAVAIR, NAVSEA, NAVWAR, ONR, SSP, and BUMED ERP business offices, and provides the NAVSUP EBO with specialized experience and expert knowledge of project management methodology and tools (Microsoft Project Professional). Herdt developed and currently maintains the EBO Integrated Master Schedule and a workload utilization matrix to determine the best way to capture data to provide a clear picture of EBO-related ERP program sustainment efforts. We plan and execute the work, measure progress, use a feedback loop to address any deviations from the plan, provide timely status reports
to leadership, and update NAVSUP and LOGCOM officials daily on the status of all assigned data elements. Herdt builds Monthly Status Reports by collecting and aggregating weekly reports about our accomplishments and level of effort to allow the Government to assess the quality of our work and provide feedback. Herdt developed ICAs and MOAs with NAVSUP’s key stakeholder partners. The ICAs describe the relationship between NAVSUP and a stakeholder’s organization regarding data items and messages passed, protocols observed, and the timing and sequencing of events to include resource “Needline” identifier, technical details, measures, and cyber classification and access control information. The MOAs describe a cooperative relationship between NAVSUP and other stakeholder(s) regarding roles, responsibilities, and communications.
Herdt recommended design changes in SAP that impact and are encoded in how NAVSUP manages business processes. These changes reflect the posting logic for how the Navy manages financial and logistics records in ERP from top to bottom of the organization. Herdt tracks, assesses, and reports defects to stakeholders. We review all system defects, assign Navy ERP scope and severity, and rigorously track the top 10 critical or high-priority defects list for all functional areas. We monitor Quality Center for defect status changes, participate in CRRB and TCCB meetings, produce minutes and review minutes for status updates. We update the QCI defect in Quality Center with accurate, detailed descriptions and attach documents to identify the issue and resolution. Herdt communicates release content to all stakeholders and extended site leads. Our UM lead sends role-based comms to end users, provides a monthly newsletter to stakeholders, and presents periodic MS Teams comms for direct feedback.
Herdt’s all-encompassing module review of SMAG business processes uncomplicated their transition into Navy ERP. We implemented new interfaces to Navy ERP for the Marine Corps Procurement Requisition System for procurement, SPS repair supply scenarios, and Master Data Repository for reporting and supply planning data.
Enterprise Support Services: Functional, Administrative, and Business Process Support
Business process support, administrative and functional support, financial operations and planning, acquisition and property management, business solutions
Herdt assisted with the coordination and dissemination of end-user communications. We provided knowledge transfer events (KTEs) to NAVSUP with a focus on the SMAG employees by providing clear, detailed step-by-step guides where appropriate, over-the-shoulder support, and observation of work. Our team collaborated with SMEs to create 30 SMAG-branded OLTs and 15 KTEs to support the implementation of new processes and functionality as well as to support the implementation of Navy ERP at the SMAG. These efforts improved the user experience and focused on transactions required to do SMAG business processes, reducing the length of each course and saving hundreds of man-hours of Government training time.
Herdt brings a disciplined and comprehensive management approach to our contracts. As prime, Herdt is solely responsible and accountable for contract performance, including any subs. Our PM maintains day-to-day technical oversight of workflow, execution, and support. Under our “One Team” model, we select the best resource for each position, emphasizing excellent support to the customer over corporate interests. To ensure the delivery of high-quality sustainment services to the SPEBO Financial Operations and Planning, Acquisition and Property Management, Business Solutions, and Customer Liaison teams and end users, our Integrated Management Framework (IMF) includes the processes, tools, and procedures we use to successfully manage the contract transition and execute tasks on schedule and within budget. The IMF organizes our methodologies, processes, procedures, and plans into an executable, tailorable approach that includes Project Management Institute (PMI) consistent management and quality methods. The IMF elements are planning, execution, progress measurement, controls and corrective action, and progress reporting. We plan and execute the work, monitor and measure progress against well-defined Acceptable Quality Levels to determine if we meet performance objectives, use our corrective action loop to address deviations from the plan, and continually and transparently report progress to our customers. We can provide qualified and experienced personnel who meet SSP labor requirements.
We are familiar with the business processes within Navy ERP that encompass settlements, surcharges, assessments, and cost transfers for the United Kingdom (UK). We identified the impact of conversion from Progress Payments to Contract Financial Payments on affected document types.
Herdt supports NAVSUP EBO financial operations and planning through our expertise with SAP FI/CO, SD, FM, and PS modules, as well as the Defense Travel System.
Herdt conducted a health assessment of NAVSUP Accounts Payable and Accounts Receivable General Ledgers (GL) to address open, aged, and dormant items from the DAR-Q and related Unmatched Transactions.
We are involved with Month End Close/Year End Close activities to ensure closing is completed promptly. Herdt’s involvement includes but is not limited to reviewing the Trial Balance to identify any Tie Point issue and recommending the necessary GL adjustments, such as Labor Accruals postings and Journal voucher postings for reconciliation, in order to proceed.
Herdt supported NAVSUP in resolving PR and PO document type errors (ZFD, Standard Procurement System [SPS], ITIMP, manual, training, shipbuilding, Military Standard Requisitioning & Issue Procedures (MILSTRIP), Organic Repair and P-Card) by correcting data elements (header, account assignment, purchasing group, funding object, ACRN, CLIN/SLIN, vendor, and item text).
We updated service entry sheets and goods receipts to resolve invoice payment issues. Herdt mapped the NAVSUP Month End Close Data Snap process to better identify and align resources along task streams, resulting in reduced execution time and increased transition speed into transactional data load file build and execution. We assisted NAVSUP in creating the first-ever mid-year conversion strategy.
Herdt spearheaded efforts to transition SMAG’s accounting methodology to Navy ERP standards, reducing hundreds of millions of dollars in balance discrepancies to a level deemed acceptable by FMO.
Herdt performed data flow mapping of Fiscal Year Dependent Master Data and wireframed the essential month-end financial and supply management processes.
Herdt created and executed an assessment of SMAG Financial and Logistics data to create the actual GL posting logic in Navy ERP. This multi-pronged Trial Balance Reconciliation process involved SMAG G8, Navy ERP T3, NAVSUP EBO, DFAS, FMO, and FMP personnel.
Herdt executed root cause analysis and reviews of all open SMAG purchase requisitions and orders, ensuring that these objects had the required data elements, were correct, and were appropriately reflected in ERP configuration.
We identified the clean-up required for non-compliant objects. The exact process was used for Sales Orders, especially regarding open quantities throughout the cutover process.
Logistics
Asset management (AM), inventory management (IM)/warehouse management (WM), acquisitions, documentation support, operating materials and supplies (OM&S), material disposition, acquisitions and property management
Herdt has two decades of experience using SAP MM (all Purchase Requisitions and Obligations Document Types), AM, IM, and WM modules to support the planning, movement, receipt, control, and issuance of physical parts for customer business operations at NAVSEA and NAVAIR Central Kiting Activity.
Herdt provided Property Management support at over 10 NSWC/NUWC sites, including Audit Readiness Support; Inventory Management (Floor-to-Book, Wall-to-Wall, Fenceline-to-Fenceline) and Automation; Material and Asset Management (Receipt and Inspection, Storage Warehousing and Issuing, and Shipping, Packaging and Crating); Material Disposition; Compliance; Knowledge Transfer and Training; Data and Metrics Analytics; Documentation Support; Operating Materials and Supplies (OM&S); and Purchase Requisition (PR) and Tech Screening Process Improvements.
Herdt developed a 40-hour course and supporting materials to accommodate the NAVSEA WFC AM and IM/WM go-lives. We developed, implemented, maintained, and trained NAVSEA personnel through Navy ERP OM&S suite Instructor Led Training courses, including warehouse operations and supervision, material movement operations and supervision, and physical inventory operations and supervision. We created course structures, narratives, process flows, screenshots, and simulations to ensure the user received the best training. We periodically performed audits on training courses to ensure compliance with the latest business rules and policy updates. The course content, simulations, and process flows were also refreshed based on training audits. Herdt developed and conducted IM/WM training for new contract employees for our Norfolk warehouse supporting NSWCPD. We developed training materials and trained new contract employees on the NSWC OM&S process and Navy ERP IM/WM functionality both in Philadelphia and Norfolk.
Financial/Audit Readiness
Audit readiness support
Herdt was integral to the NAVSUP Working Groups to help the Command achieve audit readiness goals for inventory, OM&S, and General Equipment (GE). We reviewed NAVSUP and SMAG business process assessments, legacy systems, and interfaces, and reviewed Tier 3 Navy ERP FDSs that included OM&S IM/WM, PR/POs, and GE asset management. Herdt assisted NAVSUP in identifying a logistics and financial plan. Then, working with leadership, we used Lean Six Sigma methodology to establish the plant as a “gold” standard for NAVSUP. Using the processes, documentation, and training, combined with a core tiger team from the “gold” standard plant, we replicated the processes throughout NAVSUP.
Database Administration & Support
ERP database administration, sustainment support, SAP S/4HANA, data migration
Herdt is at the forefront of new ERP database technologies as we lead design, development, testing, training, deployment, and sustainment support to NFS, an SAP S/4HANA-based solution. Herdt assessed NAVSEA shipyard financial requirements, completed the data conversion from Navy “COST” (legacy financial system) to SAP S/4HANA, and successfully tested NFS in preparation for migrating it to S/4HANA.
Herdt researched Federal Logistics Information System records, troubleshooted NAVSUP master data problems, updated master data, and identified inventory adjustment requirements. Herdt resolved issues involving change notices, material creation, Cognizance Code changes, Unit of Measure disputes, Blocked Materials, Supersession/Family chains, Core Interface issues, Bill of Material support, Bill of Distribution support, and pricing topics.
Herdt provided SME support throughout the database administration and data mapping process for USMC LOGCOM SMAG, up to and including creation of test files, test execution and remediation, multiple mock data load exercises, and cutover practice. This included field-by-field analysis in each conversion program and scheduling of data events in the SMAG Cutover Plan (created and managed by Herdt). We led the creation of exit criteria for all of these events and provided process improvements to speed up the overall process. Herdt provided key measures of post-Go-Live data quality by creating a daily IDOC status report, in which all failed IDOCS were grouped and analyzed for data quality and/or subsequent correction. Herdt provided trackers for SMAG Repair Processing, highlighting weekly repair actions requiring clean-up, correction, and process improvement. Additionally, we provided Logistical Backorder and Open Stock in Transit metrics weekly to ascertain additional transactional data issues.
Herdt developed Interface Control Agreements (ICAs) and Memorandums of Agreement (MOAs) with NAVSUP’s key stakeholder partners. The ICAs describe the relationship between NAVSUP and a stakeholder’s organization regarding data items and messages passed, protocols observed, and the timing and sequencing of events to include resource “Needline” identifier, technical details, measures, and cyber classification and access control information. The MOAs describe a cooperative relationship between NAVSUP and other stakeholder(s) regarding roles, responsibilities, and communications. Herdt regularly interacts with other stakeholder organizations to provide daily updates to senior government officials and/or their designated representatives on the status of all assigned data elements.
Data Architecture & Modeling
Data architecture & modeling, configuration management (CM)
Herdt supports NFS architectural design and modeling, installation and integration support, database administration, migration of legacy data over to SAP S/4HANA, system and acceptance testing, training and operational documentation, system software design documentation and implementation of maintenance and system enhancements. This effort included supporting the development of an MBSE environment and Cameo / SysML model of the “as-is” legacy architecture to showcase the modern solution and display the technical detail of how the “to-be” solution meets and exceeds all application requirements.
Herdt, as a subcontractor, developed, and tested a successful General Fund Enterprise Business System (GFEBS) Continuity of Operations (COOP) proof-of-concept for SAP database and SAP applications (non-database) using two non-production instances, ultimately proving that the GCSS-Army solution could keep all data synchronized across two sites. Herdt integrated GFEBS Functional Design Specifications and Application Link Enabling configuration/implementation of the Disaster Recovery (DR) solution.
Analysis and Testing
Requirements analysis, testing, deficiency identification, issue resolution
Herdt SMEs bring expertise to access, retrieve, and analyze crucial documents using industry-standard tools such as Adobe Acrobat, Excel, Access, Power BI, MS Office 365, and specialized platforms like ADVANA/JUPITER, and to translate the results directly into executive and workforce related reports, charts, and dashboards. We loaded extracted NAVSUP and SMAG data into warehouse database tables using ETL tools such as SAP Data Services or Informatica. We made them available for querying combinations with PL/SQL. The data was then incorporated into reporting tables with stored procedures or queries produced with tools such as SAP Business Objects Universe and Web Intelligence. We successfully retrieved and analyzed KSDs for CNRF, NAVSUP, and LOGCOM. Our proficiency in KSD analysis and reporting contributed to establishing the CNRF Command Improvement & Review Program.
Herdt provided key measures of SMAG post-Go-Live data quality by creating a daily IDOC status report, in which all failed IDOCS were grouped and analyzed for data quality and subsequent correction. Herdt provided trackers for SMAG Repair Processing, highlighting repair actions requiring clean-up, correction, and process improvement every week. We provided Logistical Backorder and Open Stock in Transit metrics weekly to ascertain additional transactional data issues.
Herdt data analytics personnel are recognized SMEs in MS Excel, Access, Power BI, and ADVANA/JUPITER, ensuring comprehensive and accurate data analysis from diverse sources. They bring expertise in accessing, retrieving, and analyzing crucial documents using industry-standard tools such as Adobe Acrobat, Excel, Access, Power BI, MS Office 365, and specialized platforms like ADVANA/JUPITER, and translating the results directly into executive and workforce-related reports, charts, and dashboards.
Herdt has extracted, queried, merged, analyzed, and reported data queries within NAVSUP and USMC LOGCOM Navy ERP and other systems, including table access transactions (ZE16), ZMON, custom ABAP data extraction programs, Navy ERP Data Management migration tools, Statistical Analysis System (SAS), Business Warehouse self-service reports, and Business Objects tools or by execution of available standard and custom SAP reports.
We executed DoD Activity Address (DoDAAC)/RIC/Plant Transitions for existing sites by providing ERP data pulls, performing data comparisons, identifying data cleansing issues, and providing inventory valuation and plant extension files for load to ERP. We reviewed/coordinated interfaces to external systems for multiple implementations, including Navy ERP and NFS.
We performed data analysis to identify potential issues with Transactional Data loads before and during catch-up activity, resulting in the identification and loading of nearly 900 new Sales Orders, Standard Document Numbers on all converted purchase requisitions (PRs) were reloaded, and repair transaction monitoring identified additional inventory gains for loading.
We successfully retrieved and analyzed KSDs for CNRF, NAVSUP, and LOGCOM. Our proficiency in KSD analysis and reporting contributed to establishing the CNRF Command Improvement & Review Program.
Herdt loaded extracted NAVSUP and SMAG data into warehouse database tables using ETL tools such as SAP Data Services or Informatica and made them available for querying combinations with PL/SQL.
Herdt applied our knowledge of complex Navy business processes, Navy ERP master and transactional data, data structures, and migration techniques to build targeted queries on extracted data while envisioning the end reporting product.
Herdt produced data for NAVSUP using Navy ERP transactions such as Data Browser (ZE16), ZMON, custom ABAP data extraction programs, Navy ERP Data Management migration tools, or by execution of available standard and custom SAP reports. Our Business Intelligence experts extracted, queried, merged, and reported data from many disparate data sources and translated the results directly into executive and workforce related reports, charts, and dashboards. We loaded the extracted data into warehouse database tables using ETL tools such as SAP Data Services or Informatica and made available for querying combinations with PL/SQL. The data was then incorporated into reporting tables with stored procedures or queries produced with tools such as SAP Business Objects Universe and Web Intelligence.
Herdt identified NAVSUP financial and contracting issues after analyzing 12 months of Realtime Reutilization Asset Management data issues to determine what financial effects there are for initial outfitting requirements and how Moving Average Cost value is established when the customer is a Navy Working Capital Fund activity.
Herdt wrote, executed, and analyzed queries within NAVSUP and USMC LOGCOM Navy ERP and other systems, including table access transactions (ZE16), Statistical Analysis System (SAS), Business Warehouse self-service reports, and Business Objects tools. We executed Department of Defense Activity Address (DoDAAC)/RIC/Plant Transitions for existing sites by providing ERP data pulls, performing data comparisons, identifying data cleansing issues, and providing inventory valuation and plant extension files for load to ERP. We reviewed/coordinated interfaces to external systems for multiple implementations including Navy ERP and NMMES Financial System (NFS).
We performed data analysis to identify potential issues with Transactional Data loads prior to, and during catch-up activity, resulting in the identification and loading of nearly 900 new Sales Orders, Standard Document Numbers on all converted purchase requisitions (PRs) were reloaded, and repair transaction monitoring identified additional inventory gains for loading. Herdt supported NAVSUP in resolving PR and PO document type errors (ZFD, SPS, ITIMP, manual, training, shipbuilding, Military Standard Requisitioning & Issue Procedures (MILSTRIP), Organic Repair and P-Card) by correcting data elements (header, account assignment, purchasing group, funding object, ACRN, CLIN/SLIN, vendor, and item text). We updated service entry sheets and goods receipts to resolve invoice payment issues. Herdt executed root cause analysis and reviews of all open USMC LOGCOM SMAG purchase requisitions and orders, ensuring that these objects had the required data elements, that they were correct, and were reflected properly in ERP configuration. We identified clean up required for non-compliant objects. The same process was used for Sales Orders, especially regarding open quantities throughout the cutover process.
Training & Knowledge Management
Training management & support, training curriculum management, master training schedule management
Herdt is a recognized Navy ERP master training provider, from the DON’s most senior levels to Navy and Marine Corps end users. We have developed and provided training services for multiple commands on various SAP modules and platforms (ECC and S/4). Herdt’s Training Development Team was instrumental in implementing SAP Enable Now for the Navy. We leveraged our experience implementing similar training development tools to test the SAP Enable Now functionality, provided feedback on the implementation strategy, and shared best practices.
Our Team created over 650 uPerform simulations for NAVSUP and then validated that all simulations and work instructions were correctly migrated to the SAP Enable Now server. These 650 simulations allow end-users to practice executing Navy ERP transactions independently whenever and wherever needed, eliminating the need to develop and maintain data in the Navy ERP Training Environment.
Herdt developed two new Knowledge Management templates for use with SAP Enable Now and created an SAP Enable Now eLearning Course Authoring Reference Guide and a NAVSUP SAP Enable Now Simulation Recording and Editing Guide.
Our Training Development Team enabled the NAVSUP EBO to transition from labor-intensive instructor-led training to online training by creating 63 role-based Online Training (OLT) and Self-Help Material based courses for the highest demand roles within Navy ERP.
We created a new OLT course template for SAP Enable Now using features such as pop-up glossary terminology, new interactions for knowledge checks such as drag and drop, sequencing, and matching, and PDF Student Guide that participants can save within the online course. The new template was streamlined based on end-user and SME feedback and contained 25% fewer “boilerplate” pages than the previous uPerform template, providing a more concise online learning experience.
Herdt created 30 SMAG-branded OLTs and 15 KTEs to support the implementation of new processes and functionality and the implementation of SMAG’s Navy ERP. We improved the user experience and focused on transactions required to execute SMAG business processes – reducing the length of each course and saving hundreds of man-hours of Government training time.